The Art of Casting Aluminum: Grasping the Refine
The Art of Casting Aluminum: Grasping the Refine
Blog Article
Opening the Prospective of Light Weight Aluminum Casting: A Comprehensive Introduction
Light weight aluminum casting stands as a cornerstone in the realm of metalworking, supplying a wide variety of benefits and applications throughout different industries. As we navigate with the landscape of aluminum casting processes and delve right into the intricacies of quality control procedures, an extensive introduction of unlocking the true capacity of this steel emerges.

History of Aluminum Casting
Aluminum spreading has an abundant historic history that goes back to ancient civilizations, showcasing the enduring relevance of this metallurgical process in different sectors. When ancient people like the Egyptians and the Sumerians used simple approaches to cast little items, the roots of aluminum spreading can be mapped to about 5,000 B.C.. It was not till the 19th century that light weight aluminum spreading saw significant developments with the discovery of the Hall-Héroult process for extracting aluminum from its ore, making it much more available for casting objectives.
Throughout the Industrial Change, light weight aluminum spreading acquired widespread appeal because of the metal's lightweight residential or commercial properties and rust resistance. This resulted in its considerable use in making parts for numerous sectors, including automobile, aerospace, and building and construction. The flexibility of light weight aluminum spreading enabled complex styles and complex forms to be generated with accuracy, better fueling its fostering across different fields. Today, aluminum spreading remains to be a cornerstone in the production of a vast array of products, highlighting its enduring legacy and significance in modern manufacturing processes.
Advantages and Applications
With its outstanding strength-to-weight proportion and exceptional thermal conductivity, light weight aluminum spreading provides a myriad of advantages and diverse applications throughout various sectors. One of the key advantages of aluminum spreading is its light-weight nature, making it a suitable selection for sectors where weight reduction is essential, such as automobile and aerospace.
In terms of applications, light weight aluminum casting is extensively made use of in the automobile sector for components like engine blocks, cylinder heads, and wheels due to its strength and lightweight residential properties. The convenience of light weight aluminum casting expands to customer electronics, where it is used in the production of cases and warm sinks.
Types of Light Weight Aluminum Spreading Procedures
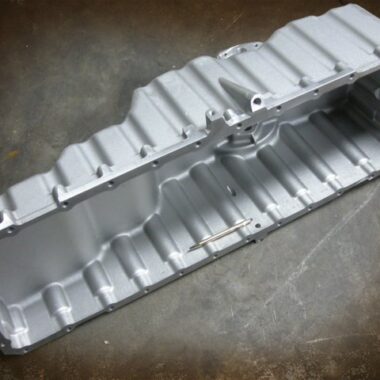
Among the different techniques employed in commercial settings, light weight aluminum casting procedures include a variety of methods matched to different applications and demands. One of the most common methods is sand spreading, where a mold and mildew is produced by compacting sand around a pattern of the desired component. This procedure is cost-effective and flexible, making it preferred for both tiny and massive production. Another extensively used strategy is die spreading, which involves compeling molten light weight aluminum right into a mold and mildew tooth cavity under high pressure. Pass away spreading enables high accuracy and repeatability, making it ideal for producing intricate forms with slim walls. Investment spreading, likewise called lost-wax spreading, her latest blog is preferred for its ability to produce complex and in-depth get rid of a smooth surface area coating. Lastly, permanent mold and mildew casting includes making use of reusable metal molds to develop premium and constant aluminum parts. Each of these aluminum casting processes uses special benefits, dealing with a large range of commercial needs.
Innovations in Aluminum Spreading Methods
Recent improvements in light weight aluminum spreading methods have actually reinvented the manufacturing sector, supplying enhanced effectiveness and accuracy in the production of facility parts. One significant advancement is the development of 3D sand printing modern technology, which allows the production of intricate sand mold and mildews with very little hands-on labor. This technique enables higher style flexibility and faster manufacturing cycles, making it excellent for prototyping and small batch production.
Moreover, the usage of innovative simulation software application has actually considerably enhanced the spreading procedure by enabling engineers to maximize mold layouts and forecast potential issues before production begins (casting aluminum). This results in boosted item quality and lowered material waste
In addition, the fostering of vacuum-assisted light weight aluminum spreading has actually improved the total quality of castings by reducing porosity and making sure a more consistent distribution of molten steel. This technique is especially beneficial for elements that call for high architectural integrity and superior surface area coating.
Quality Assurance in Light Weight Aluminum Spreading
The advancements in aluminum spreading methods have not only improved efficiency and accuracy however have actually also highlighted the vital relevance of quality assurance in making sure the dependability and performance of cast elements. Quality assurance in light weight aluminum spreading includes a systematic method to examine the manufacturing and keep an eye on procedure, recognizing any type of deviations from set standards that could influence the last item.
One critical element of quality assurance is making use of innovative innovations such as non-destructive screening approaches like X-ray and ultrasound to discover inner issues without jeopardizing the honesty of the cast components. Additionally, carrying out extensive examination methods at different phases of production assists in identifying and rectifying problems without delay, making certain that only elements fulfilling the defined criteria are released for use.
Additionally, high quality control extends past the manufacturing procedure to encompass post-casting procedures like warmth treatment and surface completing, ensuring that the final products fulfill the desired specs. By focusing on top quality control steps, manufacturers can boost item consistency, toughness, and total consumer complete satisfaction in the world of light weight aluminum casting.
Final Thought
To conclude, light weight aluminum spreading has an abundant background and offers numerous advantages and applications across different sectors. Various types of casting procedures and cutting-edge strategies have been developed to boost the effectiveness and quality of aluminum casting. Quality control actions play a crucial duty in making sure the last items fulfill the called for criteria. Generally, aluminum casting remains to be a beneficial production image source procedure with excellent potential for additional innovations in the future.
As we browse through the landscape of light weight aluminum casting procedures and dig into the ins and outs of top quality control procedures, a comprehensive overview of unlocking the real potential of this steel emerges. It was not up until the 19th century that light weight aluminum casting saw substantial improvements with the discovery of the Hall-Héroult procedure for drawing out light weight aluminum from its ore, making it more easily accessible for casting purposes.
Amongst the different techniques used in industrial settings, light weight aluminum spreading procedures incorporate view website an array of strategies matched to different applications and demands. Financial investment spreading, also understood as lost-wax casting, is favored for its capacity to generate intricate and detailed parts with a smooth surface area coating. Different kinds of casting processes and cutting-edge techniques have actually been developed to boost the performance and quality of light weight aluminum casting.
Report this page